Junior Leela Pakanati’s self-constructed robotic arm is composed of a shoulder, bicep, forearm and hand with fingers. It performs the same functions and is similar to the size of an adult arm, but there are considerable differences — it is made of 3D printed parts and Pakanati operates it with mind control.
According to Pakanati, his creation is an interface between a robotic arm and an electroencephalogram headset, which tracks brain waves. The arm functions when the headset is placed on one’s head, and he or she thinks of a specific movement, allowing the headset to pick up the brain waves and mobilize the arm.
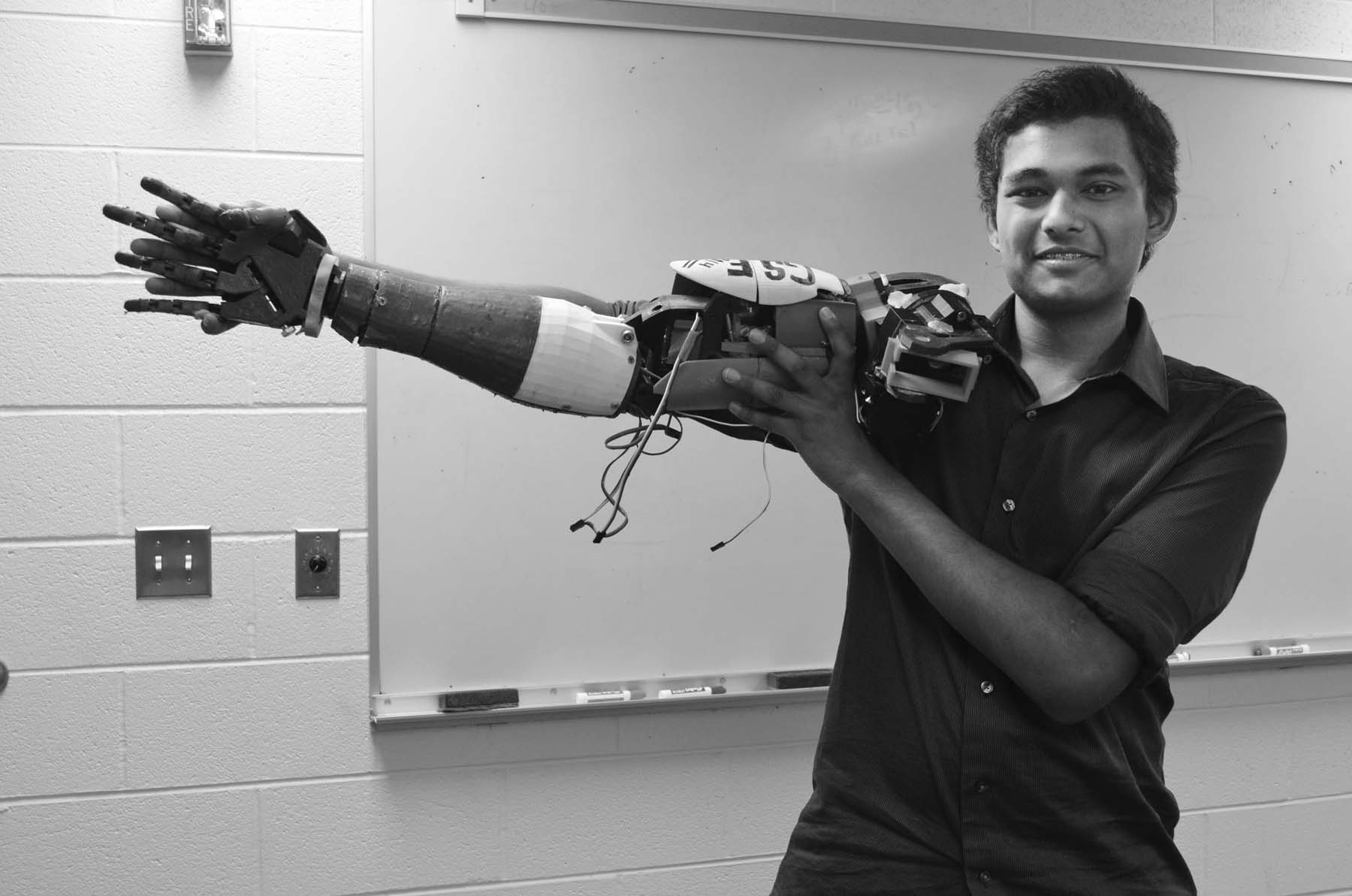
In order for the arm to learn the patterns of brain waves, Pakanati said he spent a substantial amount of time training the arm.
“I had to think a thought for eight second periods for about 20 times until [the arm] was able to recognize my thoughts so that whenever it detected that thought again, it would do a specific action,” said Pakanati. “I can open the hand, close the hand and move the bicep — things like that.”
Although Pakanati constructed the arm on his own, he said the design was not solely his. His project is mainly based off of an open source initiative called Inmoov that created a foundation for a 3D printed robot.
Pakanati began building the arm in November of 2013, but his interest in robotics was first established in middle school as a member of his school’s robotics team. He is currently an active participant in Gadget Club and has received guidance from science teacher Robert Froehlich throughout the process.
“I didn’t build any of the components,” said Froehlich. “I did, however, offer suggestions regarding the nature of a few of them.”
Froehlich said he also helped Pakanati focus on solving one problem at a time as Pakanati made many adjustments to the arm concerning stability and functionality.
“I changed the way the tendons moved with the motors,” said Pakanati. “The way the arm works is that five motors inside the forearm pull strings that would move the fingers. I changed the way that worked because before, there would be some time lag in-between the motor turning and the finger being pulled.”
Pakanati said he also altered some of the motors and gears in the upper arm as well.
Within the seven-month building process, Pakanati said he ran into various complications. A challenge he faced concerned the ability to open and close the hand.
“The string that I had that pulled the fingers open and closed would frequently break or loosen up,” said Pakanati. “I had to cut [the string], add more and then tie it all up again. In the end, I replaced the entire system with a new type of string.”
The new string Pakanati decided to use was 200-pound strength cavalier thread. Another material he used was Plasti Dip, which is a “spray paint” that adds a rubber coating to the plastic, giving the fingers the ability to grip onto objects.
According to Pakanati, the cost of his project was very little compared to prominent research projects such as the Defense Advanced Research Projects Agency, whose labor, equipment and research budgets total up to be “hundreds and thousands to millions of dollars.”
“My arm itself cost about $195 to $200 and the headset was $300,” said Pakanati. “In total it was under $500, and that was the goal I was going for: to make it affordable to the majority of people who need it.”
Pakanati entered his project with a series of required essays in the Google Science Fair. He said he was not named a finalist, but he remains motivated to alter the arm in the future.
“I learned about the way the brain waves work and the way they’re picked up,” said Pakanati. “I also enjoyed building the arm and seeing it actually work. It gave me confidence for future projects.”